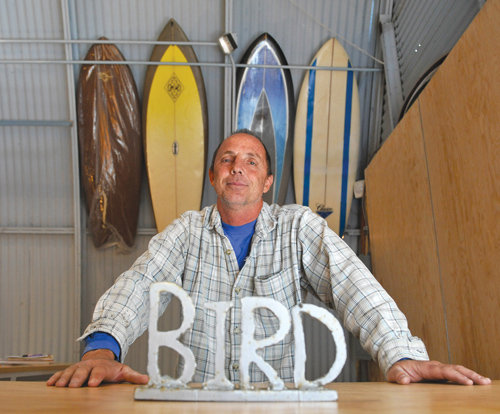
Since the latter part of the 1950s, polyurethane foam has been at the core of most all surfboards built. But after more than half a century of repeated use, surfboard technology and construction is moving toward a significant change. You may ask why has it taken so long. For starters, surfers are a notorious bunch for not accepting change, but I feel the main reason has been based upon build costs and availability of material. Having started selling boards in 1970, when prices started at under $100 for a professionally built board, I note that retail prices have not kept up with the times. Excluding the offshore-built boards of dubious design and quality, hand-built boards made right here in San Diego can cost under $500. Not much of an increase in the past 45 years when comparing the cost of goods sold in almost any other item built with so much time and effort. So why the change now? Performance is one factor. With the current level of surfing being taken to such new extremes, stronger, lighter and faster equipment becomes more sought after. With the larger surf and the radical above-the-lip surfing taking place today, boards will break at a more accelerated rate. In order to place these surfers on those waves, the board has to have improved surfing characteristics. Although an elite group truly requires these aspects, the end result is a trickle-down effect of design and technology for the average rider. Standard polyurethane foam has been the strength of a board, along with the wooden stringer that usually runs from nose to tail. The Fiberglas and resins used to seal the board from water penetration also add strength. One of the newer and strongest ways to build surfboards now relies on a lighter, expanded polystyrene foam core, vastly lighter than the traditional polyurethane blank. This is wrapped in various layers of Fiberglas and other light but high-strength materials saturated in epoxy resins. Through a practice known as vacuum bagging, the excess resin is removed under pressure in a controlled temperature setting. This basically creates a high-strength, more flexible shell surrounding the foam. This type of build, also known as sandwich construction, is superior in strength to traditional methods, and it offers up some different riding characteristics. Shelled surfboards can be built stronger and at a quicker pace than hand-built types, but this is not economically feasible in this country. There are drawbacks, to be sure. The hand-built individuality that goes into building a board is for the most part lost. The anticipation of how your custom-built craft will ride has been eradicated in exchange for the consistencies in a homogenized and mass-produced board. Whether this is a good thing depends greatly upon what surfing means to you. If you think of it as a sport, then stronger, lighter and more consistently built shelled boards might appeal to you. They will no doubt last longer and mimic the riding characteristics that are part of the board’s design. Having standardized equipment readily available to a surfer can be seen as a benefit. On the other hand, if surfing is more a part of your life in spirit and soul, you may be disappointed with the new technology. Gone is the once-in-a-lifetime feel you get only from riding a one-of-a-kind, hand- built surfboard. That magic can never be copied or duplicated.
even if all the same principal craftsman have worked on it. That magic board is just that. Magic!
Being the avid surfer I am, and having experienced all types of surfcraft and build types, I’m opting to keep a foot in both camps. Nothing will ever replace the feeling you get from riding a quality-built handmade surfboard. These types of boards are priceless. A stronger and lighter-shelled constructed board can have its place too. It is more like a tool. It’s handy to have and will more than get the job done when used properly. My advice is to try them all with an open mind. You will have to make your own call after that.